U 型弯折试验机的伺服系统对测试结果有哪些影响?
点击次数:13 更新时间:2025-07-22
控制精度决定测试参数的准确性
伺服系统的位置控制精度(通常达 ±0.01mm)直接决定弯折角度、错动位移的设定值与实际值偏差。例如,当测试要求 180° 极限弯折时,若伺服系统定位误差超 ±0.5°,会导致 FPC 实际弯折角度不足或过度,使线路承受的应力与预设值不符,误判产品耐折性能。
同时,伺服系统的扭矩控制精度(误差≤±0.1% FS)影响弯折力的稳定性。FPC 的铜箔线路、焊点在不同弯折力下的损伤阈值差异显著,伺服系统若无法稳定输出设定力值,会导致同一批次试样的受力不均,测试数据离散度增大,难以准确界定产品合格阈值。

动态响应速度影响瞬态应力模拟
FPC 在电子设备中常经历快速弯折(如手机翻盖、智能手表表冠转动),伺服系统的动态响应速度(响应时间≤5ms)决定能否模拟此类瞬态过程。响应滞后会导致实际弯折速度滞后于设定值,使 FPC 在 “加速 - 减速" 阶段承受的冲击应力与真实场景偏差,遗漏因瞬时过载导致的隐性断裂风险。
例如,测试可穿戴设备 FPC 时,若伺服系统无法跟随 100 次 / 分钟的高频弯折指令,会使实际弯折频率低于设定值,导致测试周期内的总弯折次数不足,低估产品在长期高频使用下的失效概率。

抗干扰能力保障长期测试稳定性
在持续数小时的疲劳测试中,伺服系统的抗干扰能力(如电压波动、机械振动抑制)直接影响数据重复性。若系统受电网波动影响出现转速波动(>±1rpm),会导致 FPC 在每一次弯折循环中的受力、角度出现细微差异,累积后使测试结果偏差超 5%,无法满足 ISO 18070 等标准对数据重复性(误差≤1.5%)的要求。
此外,伺服系统的闭环反馈机制(采样频率≥10kHz)可实时修正机械传动误差。当测试架因长期使用出现间隙时,系统能通过位移传感器的实时反馈调整电机输出,确保弯折轨迹始终贴合预设路径,避免因机械磨损导致的测试参数漂移。
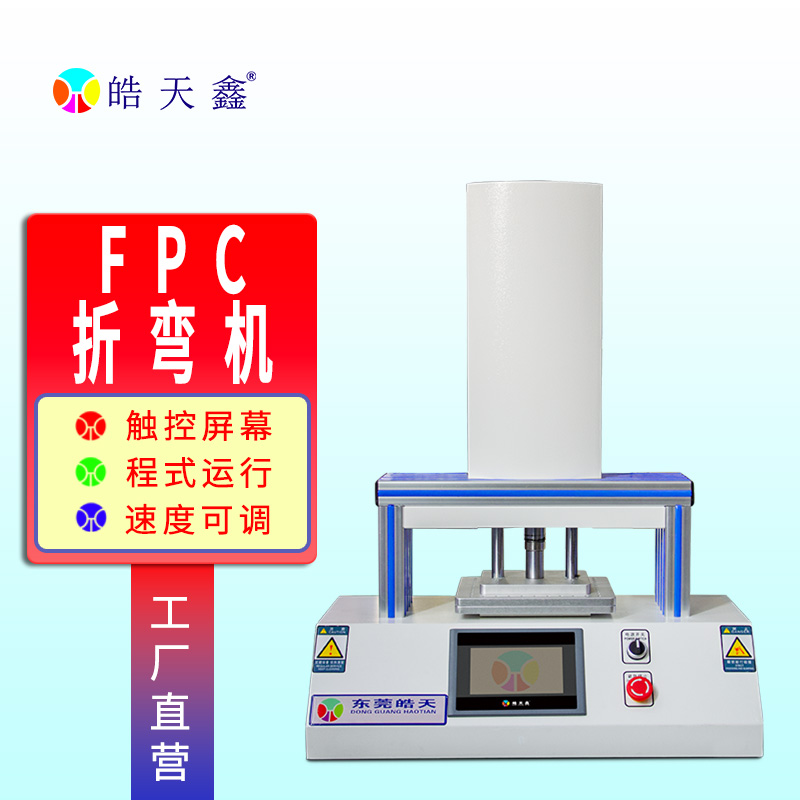
同步性控制多轴协同测试的有效性
部分 U 型弯折试验机采用双轴伺服系统(弯折轴 + 错动轴),其轴间同步精度(误差≤±0.02mm)决定复杂动作的模拟效果。例如,测试折叠屏 FPC 时,需同时实现 120° 弯折与 ±2mm 错动,若两轴运动不同步,会使 FPC 产生额外扭矩,导致线路断裂位置与实际使用中的失效点不符,误导结构优化方向。