三轴空间振动试验台的核心优势,你真的了解吗?
点击次数:66 更新时间:2025-07-09
真实工况的全息模拟能力
传统单轴设备只能进行单向振动测试,而产品在实际使用中面临的是多向力耦合的复杂环境。三轴试验台通过 X、Y、Z 三轴的协同振动,可复现 90% 以上的真实振动场景。如汽车行驶时,车身同时承受垂直路面的冲击(Z 轴)、水平转向的离心力(Y 轴)和纵向加速的推力(X 轴),这种复合振动会引发零部件的多向疲劳损伤。某测试数据显示,采用三轴设备测试的汽车悬架部件,其失效模式与实车路试的吻合度达 95%,而单轴测试仅为 68%。
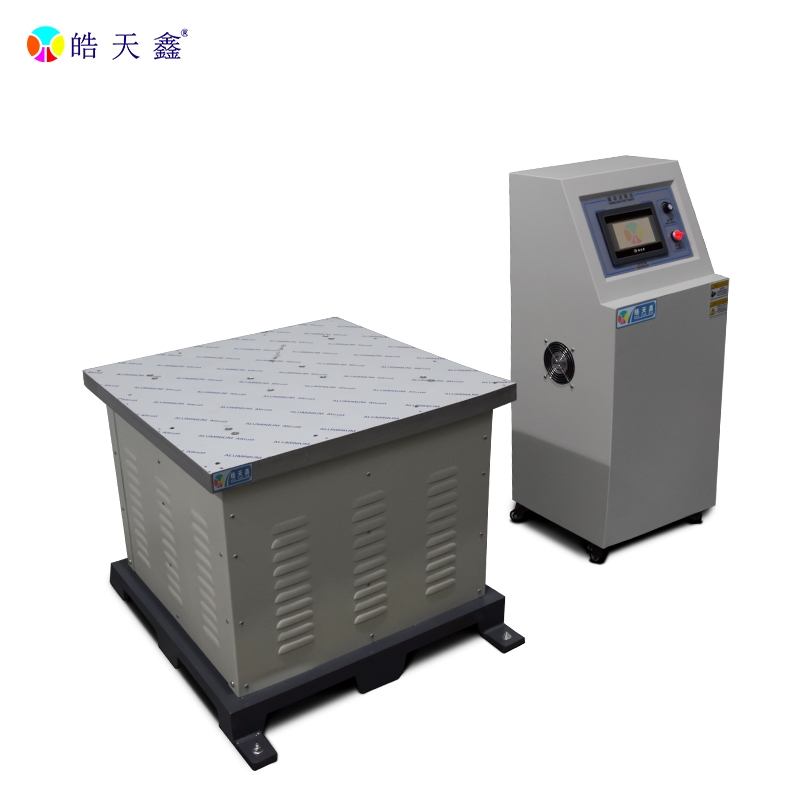
测试效率的跨越式提升
从 “分次测试" 到 “一次完成" 的转变,让测试效率实现质的飞跃。单轴设备测试多方向振动需分 3 次进行,每次调整样品安装方向至少耗时 1 小时,且多次拆装会引入 5%-8% 的误差。三轴试验台一次安装即可完成多向测试,单批次样品测试时间缩短 60% 以上。以电子元器件测试为例,传统方式测试 100 个样品需 48 小时,而三轴设备仅需 16 小时,且数据一致性提升至 98%。 数据可靠性的底层保障
多轴协同控制技术确保了测试数据的可信度。其轴间垂直度偏差≤0.05°,相位同步精度≤0.1ms,耦合干扰率≤1%,避免了虚假失效或漏检问题。在芯片封装测试中,三轴设备能捕捉到单轴测试无法发现的焊点微裂纹 —— 这些裂纹仅在特定频率的多向振动耦合下才会扩展。某实验室对比表明,三轴测试发现的潜在缺陷数量是单轴测试的 2.3 倍。

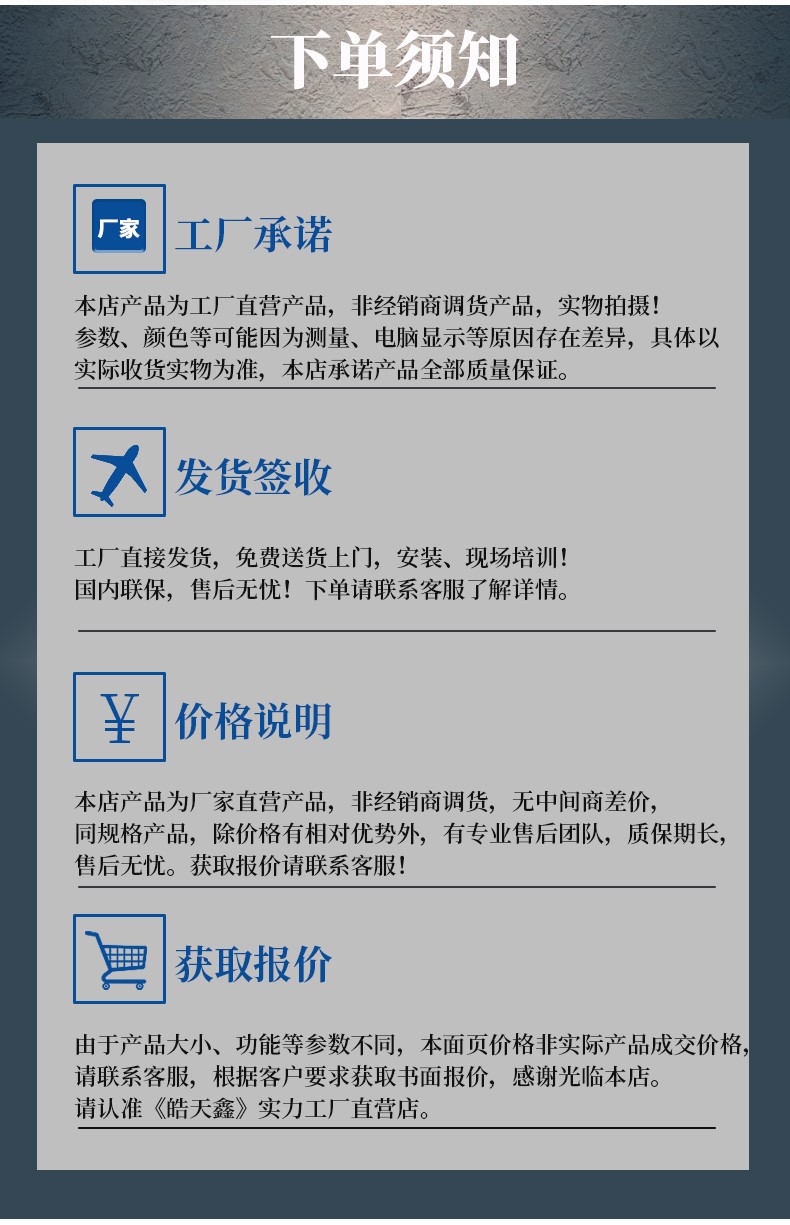
复杂测试需求的深度满足
针对航空航天、新能源等领域的特殊需求,三轴试验台展现出不可替代的优势。卫星部件测试中,可模拟发射阶段的轴向过载与横向振动复合环境;固态电池测试时,能同时施加温度循环与多向振动,精准评估条件下的性能衰减。某航天院所使用三轴设备后,卫星太阳翼展开机构的测试周期从 3 个月缩短至 1 个月,且成功发现 2 处单轴测试未暴露的结构隐患。