错动折弯测试设备的机械结构设计有哪些考量因素?
点击次数:617 更新时间:2024-11-28
一、引言
错动折弯测试设备在材料力学性能测试、产品质量检验等诸多领域都有着广泛且重要的应用。其机械结构作为设备的核心物理框架,直接决定了设备能否准确、稳定且高效地完成折弯测试任务。因此,深入分析机械结构设计中的考量因素对于提升设备性能至关重要。
二、折弯力的施加与控制
(一)动力源选择
错动折弯测试设备常用的动力源有液压系统、电动推杆等。液压系统具备输出力大、可在短时间内提供高压力的特点,适用于对较大折弯力有需求的情况,比如测试高强度金属材料的折弯性能时。而电动推杆则有着控制精度高、易于实现自动化控制的优势,更适合在需要精准控制折弯力大小以及变化速率的测试场景中应用。在机械结构设计时,需根据设备预期的应用范围和测试对象特点合理选择动力源。
(二)力的传递与调节机制
为了保证折弯力能均匀、准确地作用在测试样本上,需要精心设计力的传递路径和调节机制。例如,采用高精度的丝杆螺母副、连杆机构等进行力的传递,能够减少力在传递过程中的损耗和偏差。同时,配备压力传感器、比例调节阀等元件,可实时监测和调节折弯力的大小,以满足不同测试要求下对力的精准控制,确保测试结果的准确性。
三、运动精度保障
(一)导向机构设计
在错动折弯过程中,上下模座等关键运动部件需要沿着精确的轨迹运动,这就依赖于高质量的导向机构。常见的如直线导轨、滚珠丝杠等,它们具备低摩擦、高精度的导向特性,能够有效限制运动部件的自由度,使其仅在设定的方向上进行平稳移动,避免出现偏斜、晃动等情况,从而保障折弯角度、折弯位置等参数的精确性。
(二)传动系统精度
传动系统负责将动力源的动力传递给执行部件以实现折弯动作,其传动精度直接影响设备整体运动精度。采用精密齿轮传动、同步带传动等方式时,要充分考虑传动比的合理性、齿轮的加工精度以及同步带的张力控制等因素,通过优化这些细节,减少传动过程中的间隙和误差,确保运动部件能按照预设的速度、位移等参数准确运动。
四、材料适应性
(一)不同材质的折弯特点考虑
由于测试设备需要应对多种不同材质的材料,如金属、塑料、复合材料等,它们的弹性模量、屈服强度、延展性等力学性能差异巨大。在机械结构设计时,要确保设备的折弯模具、夹具等部件能够适应这些差异。例如,对于硬度较高的金属材料,模具需要采用高强度合金钢等耐磨且硬度匹配的材料制造;而对于塑料等较软材料,则要设计相对柔和、不易损伤材料表面的夹具和折弯方式。
(二)可调节与互换性设计
为了方便对不同材质、不同尺寸的材料进行测试,机械结构应具备一定的可调节功能。比如,夹具的夹紧范围要能够灵活调整,折弯模具的形状和尺寸可以方便地进行互换,这样能在不更换整个设备的情况下,通过简单的部件更换和调节,满足多样化的测试需求,提高设备的通用性和使用效率。
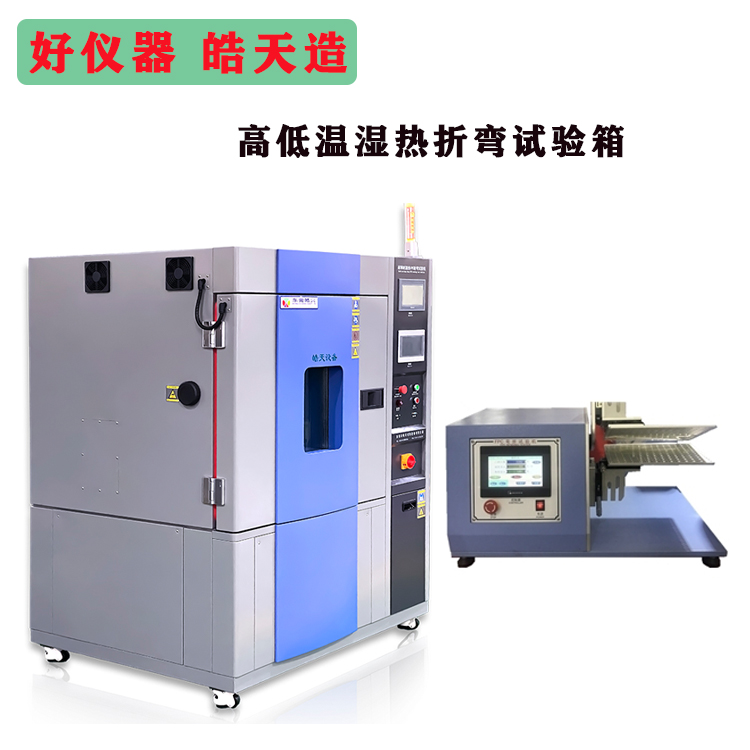
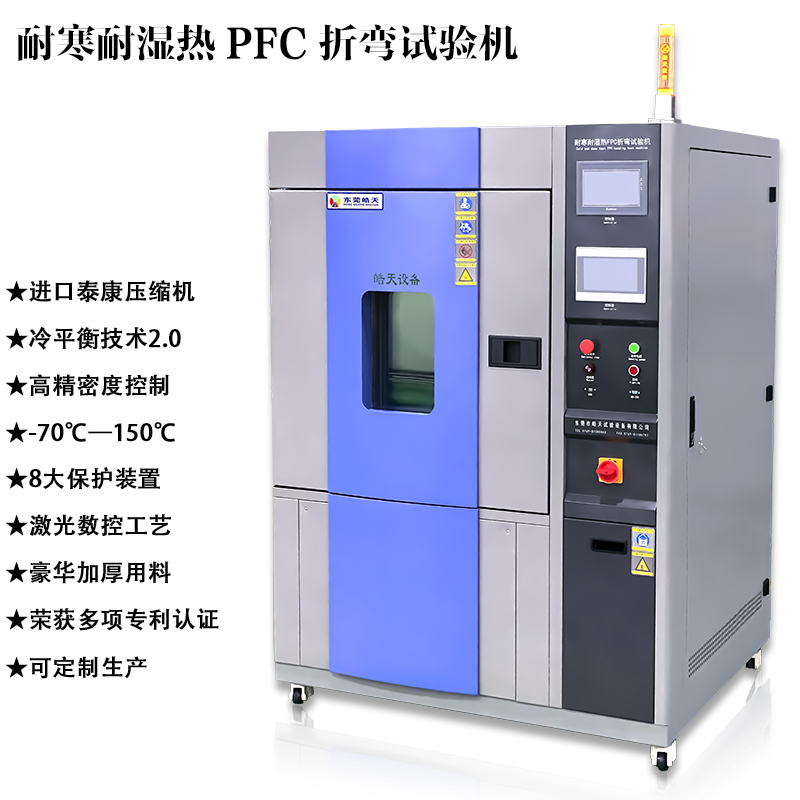
五、整体稳定性
(一)机架结构强度
错动折弯测试设备的机架作为支撑整个机械结构的基础,必须具备足够的强度和刚性。一般采用焊接结构钢或者铸造成型的方式制造机架,通过合理的结构设计,如增加加强筋、优化截面形状等,使其能够承受折弯过程中产生的各种力,防止机架出现变形、振动等情况,确保设备在长时间、高强度的工作状态下依然稳定可靠。
(二)减振与隔振措施
设备在运行过程中,动力源的运转、部件的运动等都会产生振动,这些振动不仅可能影响测试精度,还会降低设备的使用寿命。因此,在机械结构设计时,要考虑采用减振垫、隔振弹簧等装置,对关键部件进行减振处理,同时合理布局设备内部结构,减少振动的传递和叠加,营造一个相对平稳的测试环境。
六、结语
错动折弯测试设备的机械结构设计是一个综合性的工程,需要从折弯力施加与控制、运动精度保障、材料适应性以及整体稳定性等多个维度进行全面考量。只有充分兼顾这些因素,精心优化设计每一个环节,才能打造出性能优良、满足多样化测试需求的高质量错动折弯测试设备,为相关行业的材料测试和产品质量把控提供有力的技术支撑。