解析耐寒耐湿热 FPC 折弯机的热胀冷缩应对技术原理
点击次数:949 更新时间:2024-11-04
一、引言
随着电子设备在各种复杂环境下的广泛应用,对 FPC 折弯加工的要求也日益提高。耐寒耐湿热 FPC 折弯机应运而生,旨在满足在寒冷及湿热等恶劣温湿度环境中仍能实现精准、稳定折弯操作的需求。其中,热胀冷缩现象是影响折弯精度的关键因素之一,如何有效应对这一问题成为了此类折弯机技术研发的重点。
二、热胀冷缩对 FPC 折弯机的影响
(一)精度偏差
在温度变化时,折弯机的各个部件,如折弯模具、传动机构、机架等,会因热胀冷缩而发生尺寸变化。例如,在高温环境下,金属部件膨胀,可能导致折弯模具的间隙发生改变,使得 FPC 在折弯过程中的受力分布不均匀,进而引起折弯角度、折弯半径等精度指标出现偏差。
(二)机械性能变化
热胀冷缩还会影响折弯机的机械性能。低温环境下,一些材料可能会变脆,降低了部件的韧性和强度,增加了断裂的风险。同时,热胀冷缩引起的部件变形可能会导致传动机构的配合精度下降,影响折弯机的正常运行和折弯动作的顺畅性。
三、应对热胀冷缩的材料选择
(一)热膨胀系数匹配的材料
为了减少因热胀冷缩导致的尺寸差异,在折弯机关键部件的选材上,优先考虑热膨胀系数相互匹配的材料。例如,对于折弯模具,选用与 FPC 材料热膨胀系数相近的特殊合金材料,这样在温度变化时,模具和 FPC 的尺寸变化能够尽可能保持同步,从而维持相对稳定的折弯间隙和受力状态。
(二)耐温变性能优良的材料
除了热膨胀系数匹配,材料的耐温变性能也至关重要。在寒冷环境下,选用具有良好低温韧性的金属材料,如某些特种不锈钢,能够有效防止部件在低温下变脆断裂。而在湿热环境中,采用具备高防潮、耐腐蚀性能的高分子材料或经过特殊表面处理的金属材料,来保护部件免受湿气和腐蚀的侵害,同时保证其在温度变化时的尺寸稳定性。
四、结构设计层面的应对措施
(一)柔性连接与缓冲设计
在折弯机的结构设计中,采用柔性连接方式取代部分刚性连接。例如,在传动机构的连接处设置弹性元件或柔性关节,当部件因热胀冷缩发生尺寸变化时,这些柔性连接能够起到缓冲和自适应调整的作用,吸收部分变形量,避免因刚性连接导致的应力集中和部件损坏。
(二)预留伸缩空间
考虑到部件的热胀冷缩特性,在设计折弯机的机架、导轨等结构时,合理预留伸缩空间。通过精确的计算和模拟,确定在不同温湿度范围内各部件可能的尺寸变化量,并据此在结构上预留出相应的可伸缩区域,使得部件在膨胀或收缩时能够有足够的空间进行自由变形,而不会受到结构的限制产生额外的应力。
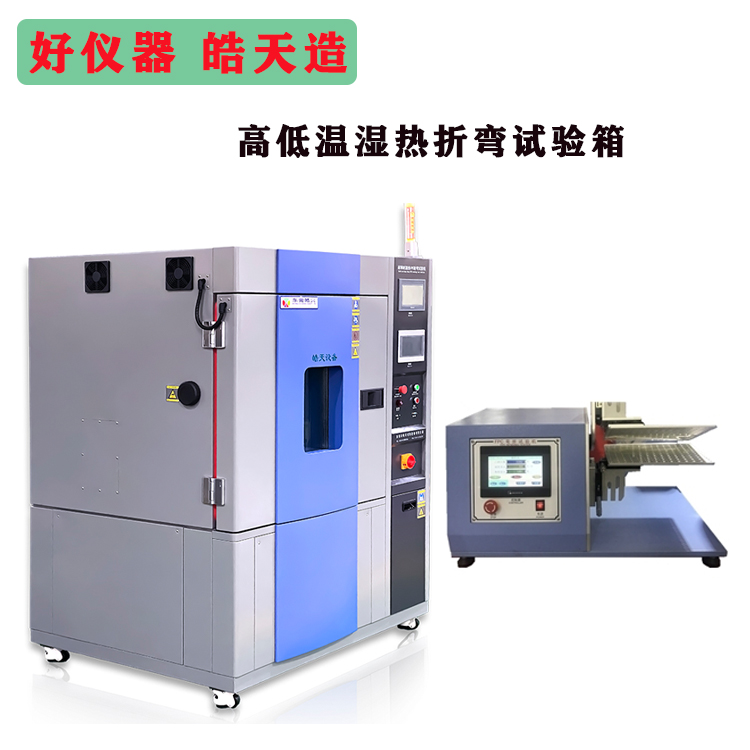
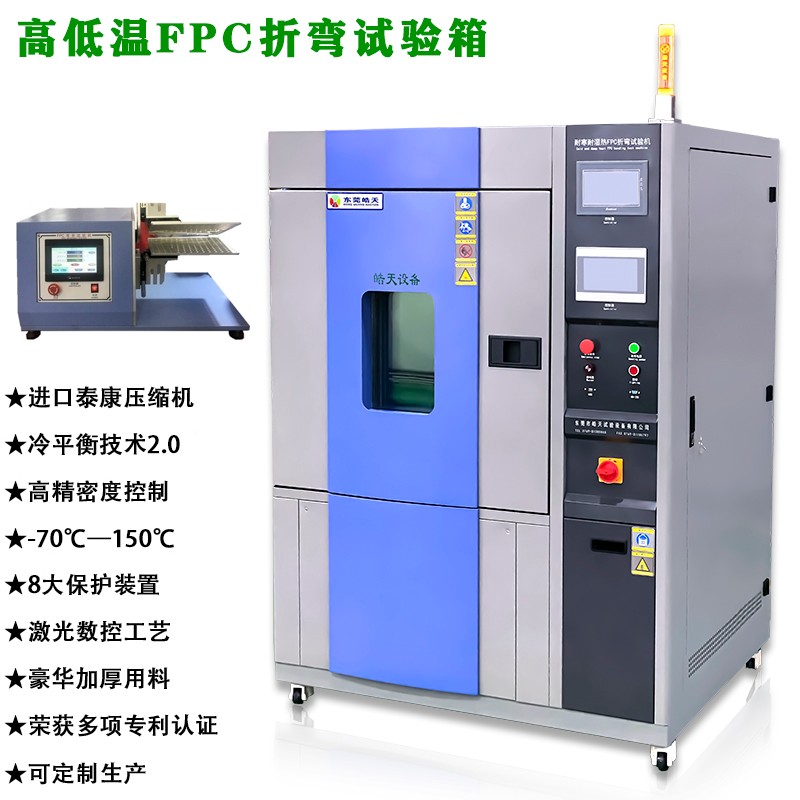
五、控制系统的热胀冷缩补偿机制
(一)温度传感器监测
折弯机配备了高精度的温度传感器,分布在各个关键部位,如折弯模具、传动机构、控制柜等。这些传感器实时监测环境温度以及各部件自身的温度变化情况,并将数据传输给控制系统。
(二)基于数据的补偿算法
控制系统根据接收到的温度数据,运用预先设定的补偿算法进行分析处理。该算法综合考虑了不同部件的热膨胀系数、当前温度与初始设计温度的差值等因素,计算出各部件因热胀冷缩而产生的尺寸变化量以及对折弯精度的影响程度。
(三)实时调整折弯参数
基于补偿算法得出的结果,控制系统能够实时调整折弯机的各项折弯参数,如折弯力、折弯速度、折弯角度等。例如,当监测到模具因温度升高而膨胀导致折弯间隙变小,控制系统会适当降低折弯力,以避免 FPC 受到过度挤压而出现质量问题;当温度降低使部件收缩时,相应地调整折弯角度以保证最终的折弯精度符合要求。
六、结论
耐寒耐湿热 FPC 折弯机通过在材料选择、结构设计以及控制系统等方面采用一系列针对热胀冷缩现象的应对技术原理,有效地克服了在寒冷和湿热等复杂温湿度环境下热胀冷缩对折弯精度和设备运行的不利影响。这些技术的综合应用使得 FPC 折弯机能够在温湿度条件下依然保持高精度、稳定的折弯作业,为电子设备制造等相关行业在不同环境下的生产提供了可靠的技术保障。随着科技的不断发展,未来对于 FPC 折弯机在应对热胀冷缩及其他环境因素方面的技术创新仍将持续推进,以满足日益提高的工业生产需求。