高温高湿 FPC 折弯试验机的能耗情况怎样?
点击次数:498 更新时间:2024-10-30
一、引言
在电子制造领域,随着柔性印刷电路板(FPC)的广泛应用,对其性能和可靠性的测试需求日益增长。高温高湿 FPC 折弯试验机作为模拟环境下 FPC 折弯性能测试的关键设备,其能耗情况不仅关乎使用成本,也与设备的运行效率及可持续性密切相关。本文将深入探讨该试验机的能耗构成、影响因素以及优化措施等方面内容。
高温高湿 FPC 折弯试验机主要通过精确控制温度、湿度以及折弯动作等参数,来模拟实际应用场景中 FPC 可能面临的恶劣环境并进行折弯测试。其通常配备有加热系统、加湿系统、折弯驱动机构以及相应的控制系统等。加热系统负责提升试验环境的温度,加湿系统用于调节湿度,折弯驱动机构则实现对 FPC 的精准折弯操作,而控制系统协调各部分协同工作,确保试验按照设定参数有序开展。
三、能耗构成分析
加热系统能耗:
加热元件:高温高湿环境的营造往往需要大功率的加热元件,如电阻丝、加热管等。这些加热元件在持续通电工作过程中会消耗大量电能,其能耗大小与加热功率、加热时间以及环境散热情况等因素密切相关。例如,若设定的试验温度较高,加热元件需长时间维持高功率输出,能耗自然会显著增加。
温控系统:为了精确控制试验温度,温控系统需要不断监测和调整加热元件的功率。虽然其自身能耗相对加热元件较小,但在长时间运行过程中,其对温度传感器、控制器等部件的供电也会产生一定的电能消耗。
加湿系统能耗:
加湿设备:常见的加湿方式包括蒸汽加湿、超声波加湿等。无论是哪种加湿方式,都需要消耗电能来将水转化为水汽并输送到试验环境中。比如蒸汽加湿需要加热水产生蒸汽,这一过程需要消耗大量的电能;超声波加湿则依靠超声波振动将水雾化,其超声发生器同样需要持续供电,能耗也不容小觑。
湿度控制:与温度控制类似,湿度控制系统要实时监测和调节湿度,确保其维持在设定范围内。这涉及到湿度传感器、控制器等部件的运行,它们也会消耗一定的电能。
折弯驱动机构能耗:
电机及传动部件:折弯驱动机构通常由电机驱动,通过传动部件如皮带、链条、齿轮等将动力传递给折弯部件,实现对 FPC 的折弯操作。电机在运行过程中会消耗电能,其能耗取决于电机的功率、转速以及负载情况等。例如,当对较厚或硬度较高的 FPC 进行折弯时,电机需要提供更大的扭矩,相应地能耗也会增加。
控制与调节:为了实现精准的折弯角度和速度控制,还需要配备相应的控制电路和调节装置。这些部件在工作过程中同样会消耗电能,尤其是在频繁调整折弯参数的情况下,其能耗可能会有所上升。
控制系统及其他辅助设备能耗:
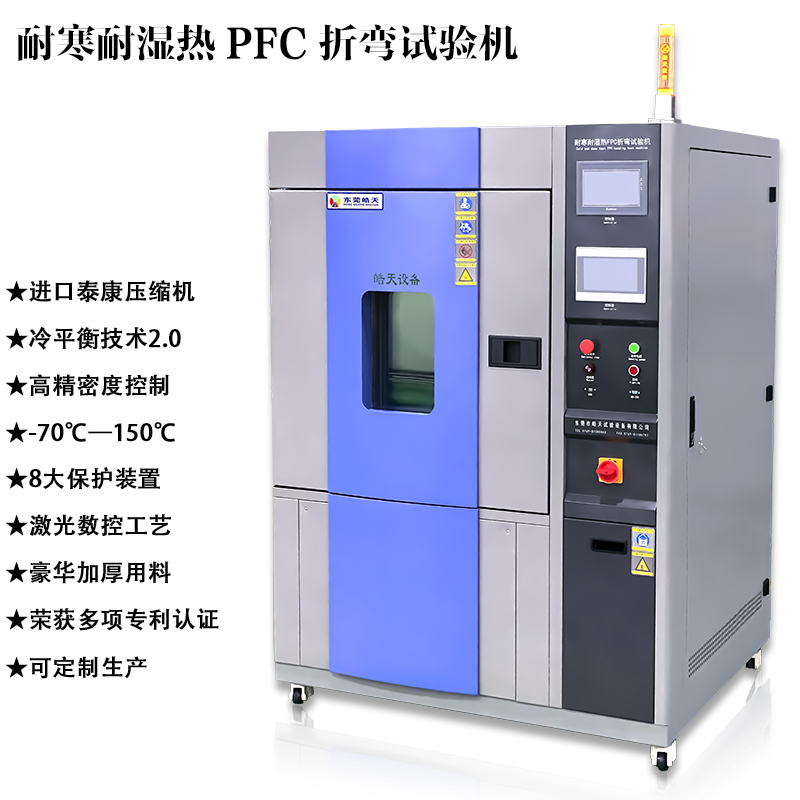
四、影响能耗的因素
试验参数设置:
温度和湿度设定:较高的试验温度和湿度要求意味着加热系统和加湿系统需要更强劲的输出,从而导致能耗增加。例如,将试验温度从 30℃提高到 60℃,加热系统可能需要成倍增加功率输出,能耗也会随之大幅上升。
折弯次数和速度:频繁的折弯操作以及较高的折弯速度会使折弯驱动机构的电机频繁运转且处于较高负载状态,进而增加其能耗。而且,更多的折弯次数意味着试验时间延长,其他相关系统如加热、加湿等也需要持续运行更长时间,整体能耗也会升高。
FPC 特性:
厚度和硬度:较厚或硬度较高的 FPC 在折弯时需要更大的力,这使得折弯驱动机构的电机需要提供更大的扭矩,从而增加了电机的能耗。同时,由于折弯难度增加,可能需要更多的试验时间来完成规定的折弯次数,进一步影响整体能耗。
材料组成:不同的 FPC 材料在高温高湿环境下的物理和化学性质不同,可能会影响试验参数的设置。例如,某些材料在高温下可能更容易变形,需要更精细的折弯控制,这可能导致折弯驱动机构和控制系统的能耗增加。
设备自身性能:
运行环境:
五、能耗优化措施
优化试验参数设置:
选用合适的 FPC 材料和特性:
提升设备自身性能:
改善运行环境:
六、结论
高温高湿 FPC 折弯试验机的能耗情况受到多种因素的综合影响,包括试验参数设置、FPC 特性、设备自身性能以及运行环境等。通过合理优化试验参数、选用合适的材料、提升设备性能以及改善运行环境等措施,可以有效降低设备的能耗,不仅能够降低使用成本,还能提高设备的运行效率和可持续性,为电子制造领域的 FPC 测试工作提供更加经济、高效的保障。